Product quality is the assurance for users and patients, the prerequisite for market penetration, and the most important factor for sustainable growth of a company. Quality Management System (QMS) is a systemic management approach involving many departments and functions in an organization and spanning the product realization process from product design and development, manufacture to servicing through documentation and record keeping to assure that product quality is maintained. ISO 13485:2016 certification or passing Medical Device Single Audit Program, (MDSAP) audit is an indication of QMS establishment, while consistent and effective implementation is critical in ensuring product quality.
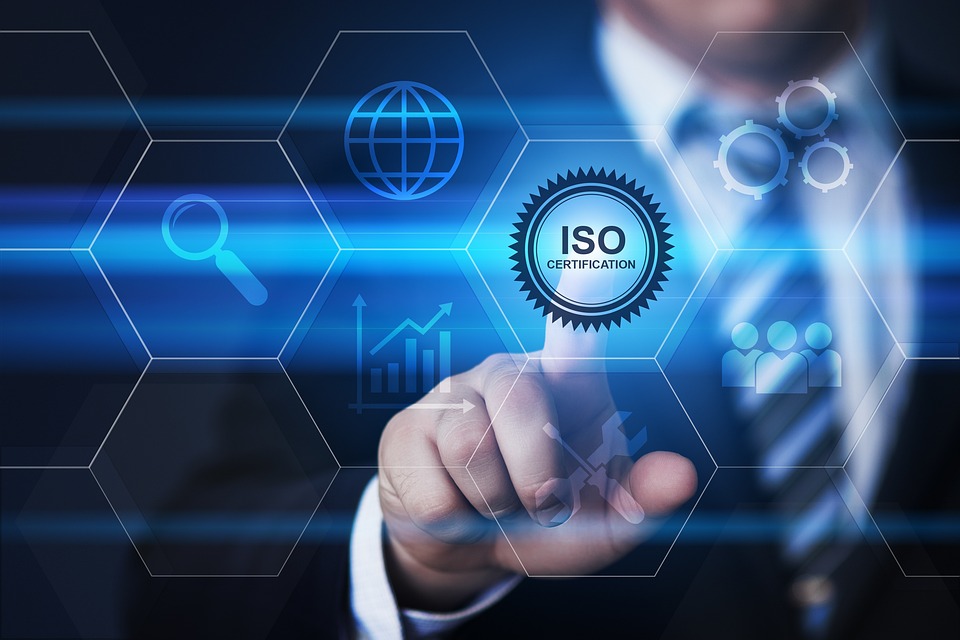
QMS Establishment & Implementation
Whether you are planning to have a quality management system (QMS) in place, or implementing a QMS in ever-expanding new exciting business areas, or looking for an e-QMS system, or designing and executing an effective employee training program, it is critical to know the requirements, start and implement in the right way, to lessen the pain and cost to have poor quality processes thus products.
Helical Sphere helps you to establish, if not in place yet, a QMS that is compliant to ISO 13485 and FDA 21 CFR 820, and/or implement any applicable sections to your product development, manufacture or post-market processes.
Helical Sphere can also help you assess your current status through quality audits to identify the gaps and future needs to further implement the system for higher levels of compliance to regulatory requirements. This will give you a head start in the preparation of meeting the requirements and obtaining US FDA product clearance and approval and EU IVDR CE mark.
QMS Improvement
Continuous improvements are the essence to ensure quality. With a running QMS, many components in the system will help to drive the improvement process. For example, nonconformance and CAPA reveal current and potential quality problems in the product development and manufacture processes, and if well-leveraged, provide opportunity to drive the improvements to find out the root cause(s) of problems so that not only the current problems are corrected but most importantly problems are prevented to happen in the future.
Helical Sphere will help you to identify problems in the quality system and processes, utilize right tools, get down to the root, and eventually improve the processes and system.
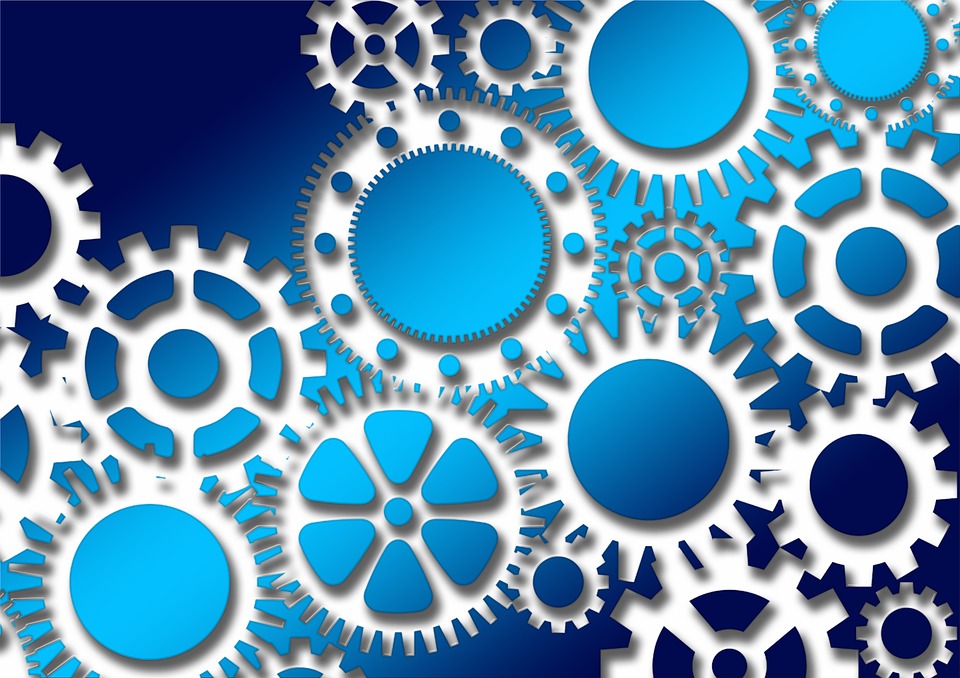
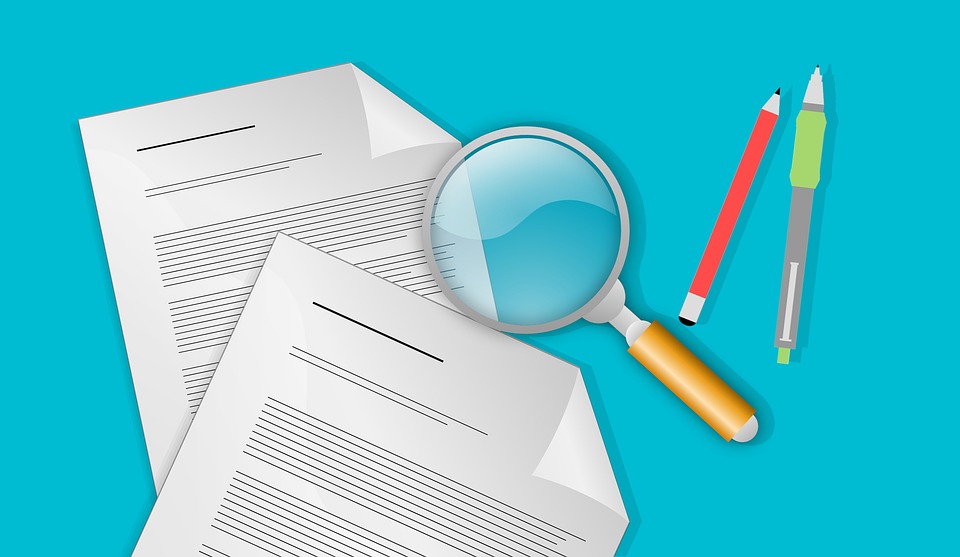
Quality Audit
Diligence in daily observing, reporting and resolving issues is an effective method, while auditing is the ultimate approach to systemically look at the entire QMS to ensure compliance. Internal audits help an organization seep through the system and processes in a systemic way throughout the time. Supplier audits ensure compliance of especially critical suppliers. Mock audits look at the QMS and relevant processes at different time points and give the organization an opportunity to have issues identified and problems solved before a real audit or inspection happens, and to practice of readiness for ISO 13485 certification or an FDA inspection.
Helical Sphere can help design and execute an internal audit plan, audit suppliers, and conduct mock audits, such as mock FDA inspection, mock ISO 13485 certification/surveillance audits, mock MDSAP audits, and mock FDA BIMO audits.